How is Nitrile Rubber Made: A Comprehensive Guide
Nitrile rubber, also known as NBR (nitrile butadiene rubber), is a synthetic rubber that has become indispensable across various industries. From automotive seals to medical gloves, its applications are vast. But how is nitrile rubber made? The production process of nitrile rubber involves several steps, each crucial for obtaining its desirable properties like oil resistance, durability, and flexibility. In this article, we will take a deep dive into the step-by-step process of manufacturing nitrile rubber and its essential uses in everyday products.
- What is Nitrile Rubber?
- Step 1: The Polymerization of Acrylonitrile and Butadiene
- Step 2: The Creation of Nitrile Rubber Latex or Solid Form
- Step 3: The Vulcanization Process
- Step 4: Post-Processing and Quality Control
- Applications of Nitrile Rubber
- FAQs About Nitrile Rubber Manufacturing
- Conclusion
What is Nitrile Rubber?
But first, let’s take a closer look at what nitrile rubber is and why its production is so popular. Nitrile rubber is a copolymer obtained from the polymerization of acrylonitrile and butadiene. Acrylonitrile provides the rubber with its oil, fuel, and chemical resistance, and butadiene provides the rubber with its flexibility. These properties make it suitable for use in high-performance applications that are prone to wear and tear in harsh chemical and oil environments.
Step 1: The Polymerization of Acrylonitrile and Butadiene
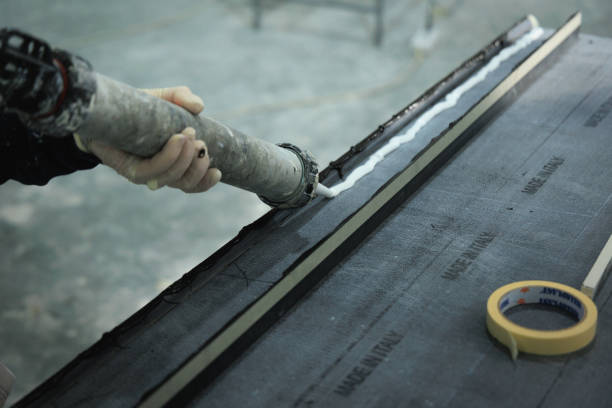
The manufacture of nitrile rubber involves the polymerization of acrylonitrile (ACN) and butadiene. This process entails the reaction of these two monomers under certain conditions using a catalyst. The polymerization reaction may be carried out in a solution or emulsion process.
and the product formed is a copolymer known as nitrile rubber. The proportion of acrylonitrile to butadiene is varied to provide the necessary level of flexibility, strength, and oil resistance.
In this step, the polymer chains that are formed are not very long, and therefore the rubber still has to undergo further processing. The important thing to note here is that the higher the percentage of acrylonitrile, the higher the chemical resistance but lower the flexibility.
Step 2: The Creation of Nitrile Rubber Latex or Solid Form
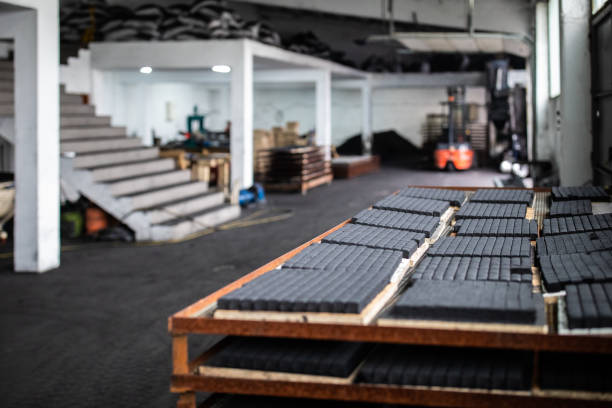
After the polymerization process is over, the next step is to process the nitrile rubber into a usable form. There are two primary forms of nitrile rubber: latex and solid rubber.
1. Latex: The polymerization process can give a latex form of nitrile rubber; this is a dispersion of the rubber particles in water. This form is used mainly in such processes as the manufacturing of gloves, where the liquid latex is poured into molds to produce thin, flexible articles.
2. Solid Rubber: In other uses, for example, in seals, hoses, and gaskets, the latex is vulcanized into solid rubber. This is done by drying or coagulating the material to obtain a solid mass of nitrile rubber, which can then be shaped and molded into different forms.
Step 3: The Vulcanization Process
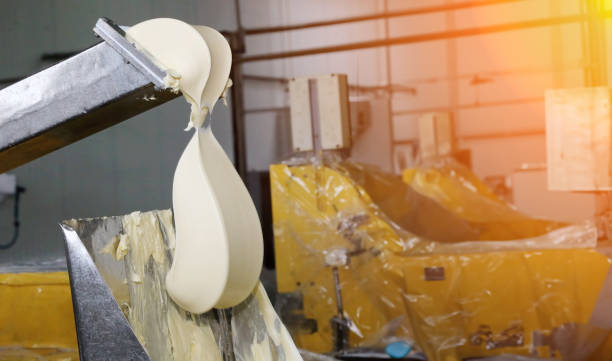
In order to make the nitrile rubber more durable and to enhance its wear-resisting properties, vulcanization is done. Vulcanization is a process of heating the rubber with sulfur or other cross-linked materials. This process forms additional covalent bonds between the polymer chains, which enhance the material’s mechanical strength, flexibility, and thermal stability. The rubber becomes much more resistant to wear and tear and can thus be used in applications that require long-lasting rubber material.
Time and temperature of vulcanization are regulated to obtain the desired characteristics of the end product, such as hardness and flexibility. In the case of medical gloves, the flexibility of vulcanization needs to be adjusted so that the gloves have enough stretch and strength, while for industrial seals, the material must be stiffer and resistant to oils.
Step 4: Post-Processing and Quality Control
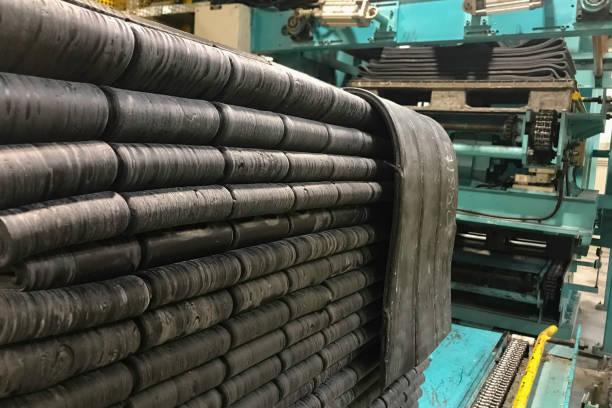
The nitrile rubber is vulcanized, and post-vulcanization treatments may include washing the rubber, drying the rubber, and then cutting the rubber to a preferred size and shape. The rubber material is also subjected to a quality check to determine it’s suitability with regards to properties such as oil resistance, tensile strength, and elongation, among others.
In automotive and healthcare industries, quality nitrile rubber cannot be compromised for any reason. Thus, the control of the quality is critical to guarantee that the characteristics of the rubber fully correspond to the demands. Automatic testing equipment is utilized to determine the chemical resistance of the rubber, the endurance of the material under stress, and its characteristics when exposed to high temperatures.
Applications of Nitrile Rubber
Due to its ability to resist oil, be very durable, and at the same time be flexible, nitrile rubber can be used in many applications. Some of its most common uses include:
1. Automotive Industry: Nitrile rubber is applied in seals, gaskets, and hoses since it can be used where fuels, oils, and high temperatures are present.
2. Medical Industry: Nitrile rubber does not swell with oils and chemicals, and that is why it is used in disposable gloves and other medical products.
3. Oil & Gas Industry: Nitrile rubber seals and gaskets are popular for sealing and to shield equipment from oil and chemical contamination.
4. Consumer Products: Nitrile rubber is also used in products that are used in day-to-day life, such as soles of shoes, balloons, and glue.
FAQs About Nitrile Rubber Manufacturing
Q1: What makes nitrile rubber resistant to oils?
A1: Nitrile rubber's high acrylonitrile content makes it resistant to oils, fuels, and other chemicals by reducing the material’s interaction with hydrocarbons, ensuring durability.
Q2: How is nitrile rubber different from natural rubber?
A2: Unlike natural rubber, which is derived from latex, nitrile rubber is synthetic and offers better resistance to oils, fuels, and chemicals, making it ideal for industrial applications.
Q3: Can nitrile rubber be recycled?
A3: Nitrile rubber can be recycled, but it requires specialized methods. The process involves breaking down the material into smaller particles, which can be repurposed for lower-value products.
Q4: What industries use nitrile rubber?
A4: Nitrile rubber is widely used in the automotive, medical, oil & gas, and consumer goods industries, particularly for products that require oil resistance and durability.
Conclusion
In conclusion, nitrile rubber is a versatile material that is synthesized through polymerization, vulcanization, and post-treatment. Its ability to withstand oils and chemicals, its durability, and its flexibility make it a versatile material in many industries, including automotive and medical. In many cases, nitrile rubber is the material of choice, whether you require a high-performance seal or medical gloves.
Why choose nitrile rubber from FUNAS?
Foam rubber supplier FUNAS provides the best quality insulation material and superior wholesale insulation material, such as nitrile rubber. FUNAS focuses on the quality and the performance and guarantees that your needs are satisfied with high accuracy. For more information, please come to FUNAS and check out our extensive line of quality products.
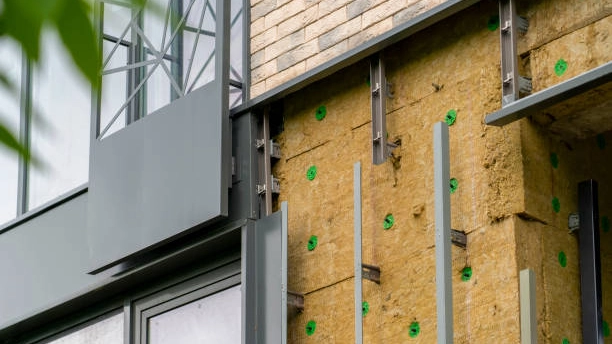
Does Heat Insulation Work? The Ultimate Guide to FUNAS Insulation Solutions
What is the cheapest way to insulate internal walls? | FUNAS Guide
How thick is acousticlining? | FUNAS Guide
What are the disadvantages of thermal insulation? | FUNAS Guide
How much does acousticfoam reduce sound? | FUNAS Guide
FAQ
How to start a consultation?
You can contact us through our website, phone, or email. We will arrange a professional staff to discuss your needs about best thermal insulator and how we can help you.
What is the typical delivery time for custom orders?
Our daily production capacity is 800 cubic meters. Delivery time varies depending on the complexity of the insulation material wholesale order, but we can deliver large quantities of customized products within 4-6 weeks after the approval date, and small quantities can be delivered within 15 days.
service
Are your rubber foam products environmentally friendly?
Yes, our insulation products are designed with sustainability in mind. They help reduce energy consumption by minimizing heat loss and gain, and they are made from durable materials that have a long life cycle, reducing the need for frequent replacement.
What types of rubber foam insulation products do you offer?
We offer a wide range of rubber foam insulation products, including custom shapes and sizes, thermal and acoustic insulation solutions, and options with specialized coatings such as flame retardancy and water resistance. Our products are suitable for applications in HVAC, automotive, construction, and more.
How does your technical support work?
Our technical support team is available to guide you through every stage of your project—from product selection and design to installation. We provide expert consultation to ensure that you get the best insulation solution for your needs and can assist with troubleshooting if needed.
You might also like
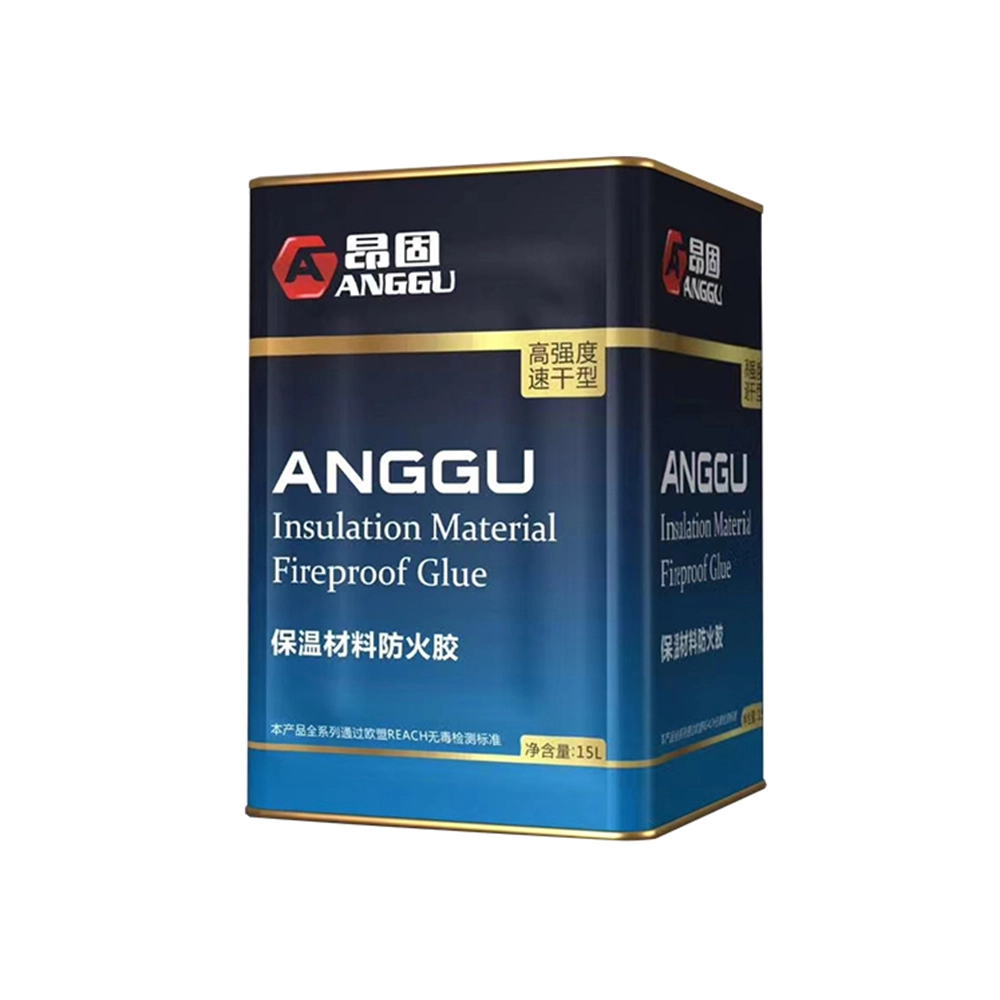
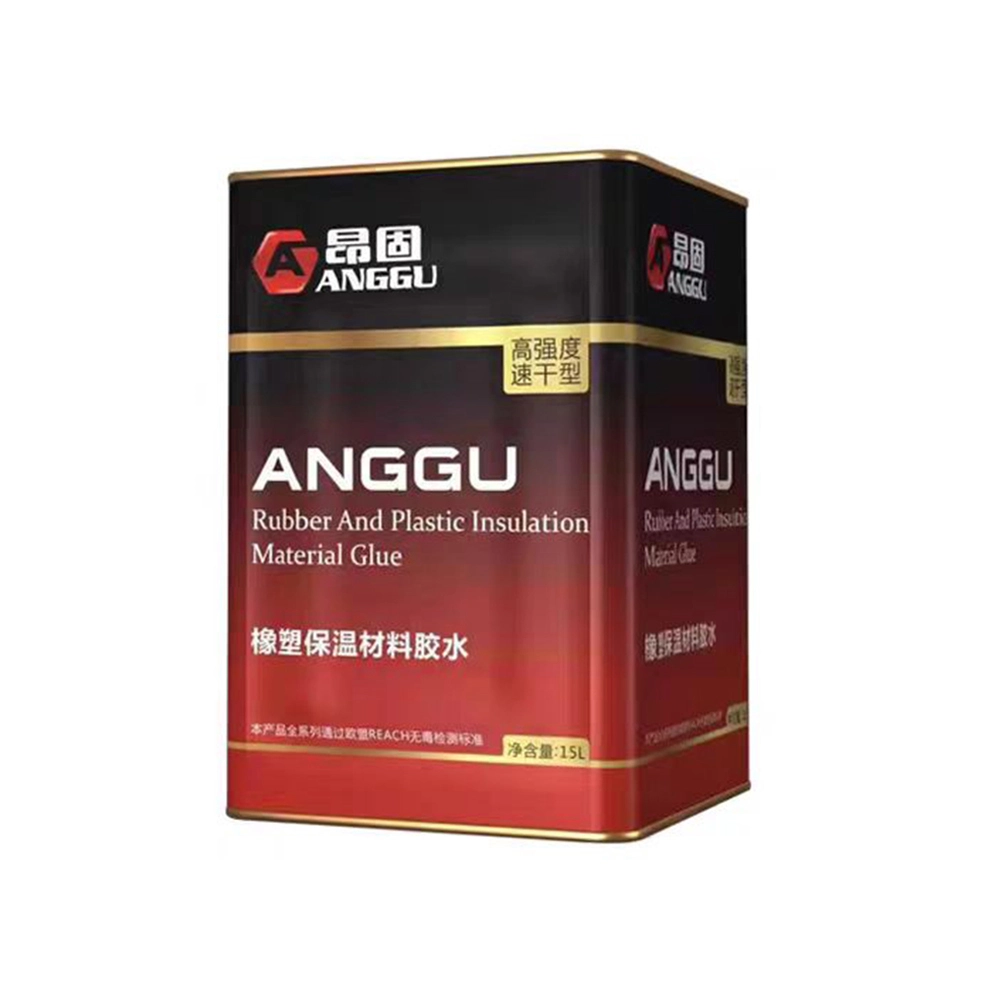
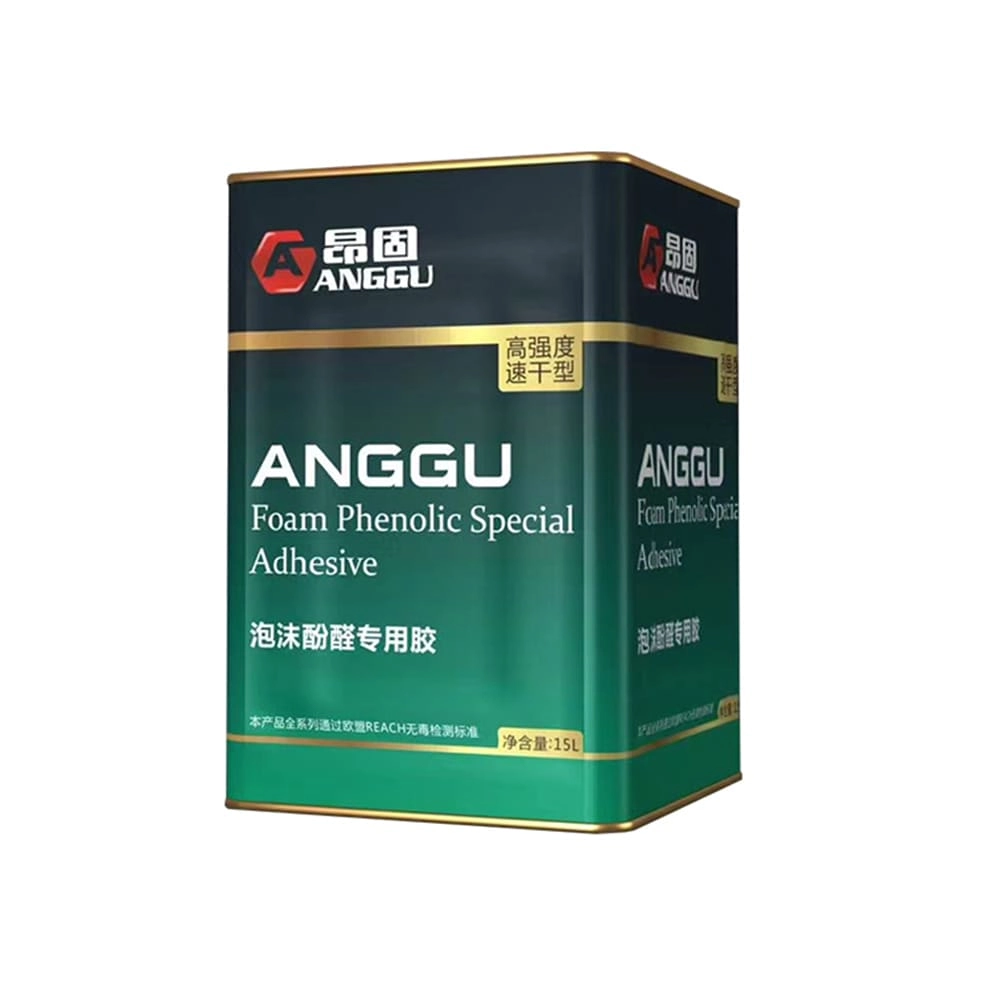
This product has passed the national GB33372-2020 standard and GB18583-2008 standard. (The product is a yellow liquid.)
Anggu foam phenolic glue is a kind of glue with corrosion resistance, low odor, high strength and excellent brushing property. Can be sprayed for construction with fast surface drying speed, long bonding time, no chalking and convenient operation.
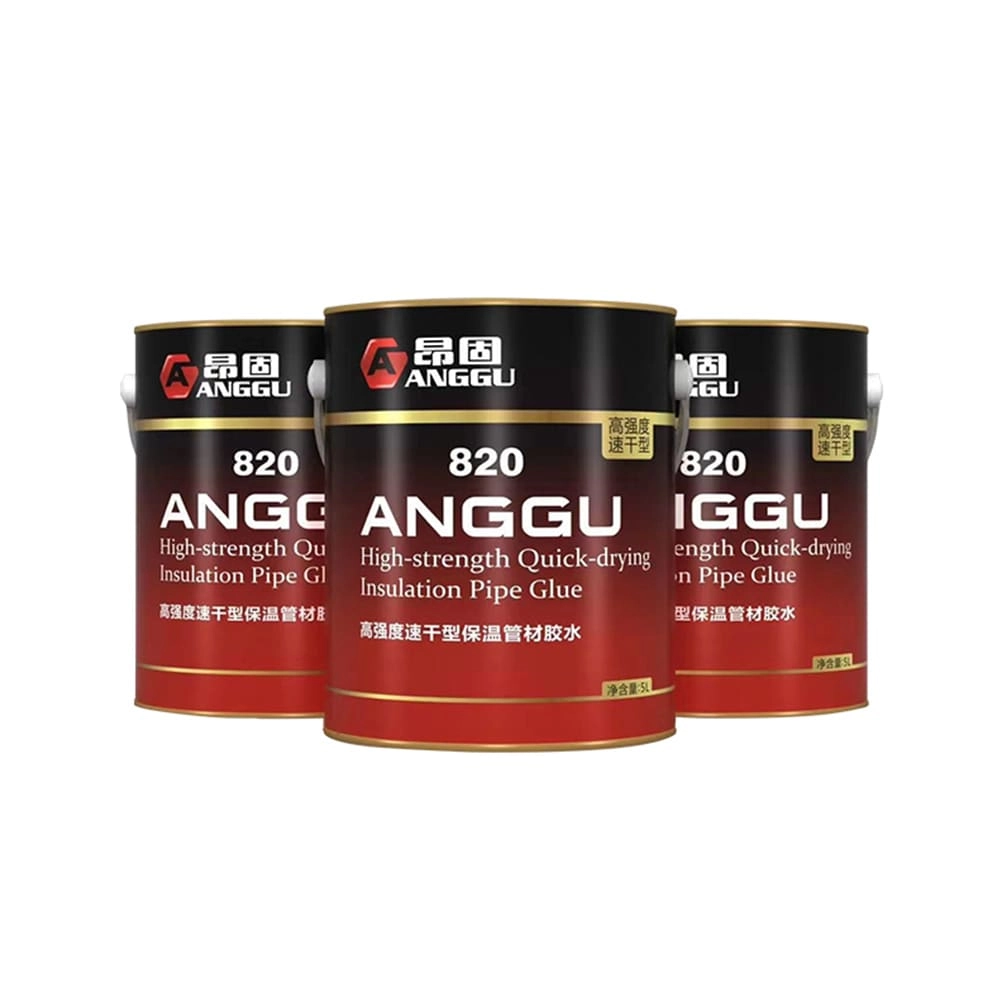
This product has passed the EU REACH non-toxic standard, ROHS non-toxic standard. (The product is black glue.)
Anggu 820glue is a low-odor, high-strength quick-drying glue; Fast drying speed, long bonding time, no powder, non-toxic.
Discover the future of energy efficiency with FUNAS's "Top Thermal Insulation Materials List for 2025." Our expertly curated list highlights innovative solutions perfect for your construction and renovation needs. Stay ahead of the curve with cutting-edge insulation technology designed for optimal thermal performance and sustainability. Trust FUNAS for advancements that redefine comfort and efficiency in every project.
Leave a message
Have any questions or concerns about our products? Please leave us a message here and our team will get back to you promptly.
Your queries, ideas, and collaboration opportunities are just a click away. Let’s start a conversation.